Comprehensive Overview: What is Porosity in Welding and Just How to avoid It
Comprehensive Overview: What is Porosity in Welding and Just How to avoid It
Blog Article
Porosity in Welding: Identifying Common Issues and Implementing Finest Practices for Avoidance
Porosity in welding is a pervasive problem that typically goes undetected until it causes substantial troubles with the stability of welds. This common flaw can jeopardize the stamina and sturdiness of bonded frameworks, posing safety and security dangers and resulting in pricey rework. By comprehending the origin creates of porosity and carrying out efficient prevention methods, welders can considerably improve the top quality and dependability of their welds. In this conversation, we will certainly explore the crucial elements adding to porosity development, analyze its harmful results on weld efficiency, and discuss the most effective practices that can be embraced to minimize porosity event in welding processes.
Typical Causes of Porosity

Utilizing unclean or wet filler products can present contaminations right into the weld, adding to porosity problems. To reduce these typical reasons of porosity, extensive cleaning of base steels, correct securing gas selection, and adherence to optimum welding criteria are important methods in achieving top quality, porosity-free welds.
Impact of Porosity on Weld Quality

The visibility of porosity in welding can considerably jeopardize the structural honesty and mechanical buildings of bonded joints. Porosity creates voids within the weld steel, deteriorating its overall stamina and load-bearing ability.
Among the primary consequences of porosity is a reduction in the weld's ductility and durability. Welds with high porosity degrees have a tendency to exhibit reduced impact stamina and lowered capacity to warp plastically prior to fracturing. This can be particularly concerning in applications where the welded parts are subjected to dynamic or cyclic loading problems. Additionally, porosity can hamper the weld's capacity to successfully transmit pressures, bring about premature weld failure and possible safety and security hazards in important structures.
Best Practices for Porosity Avoidance
To improve the structural honesty and top quality of welded joints, what particular measures can be applied to decrease the occurrence of porosity throughout the welding procedure? Making use of the proper welding strategy for the certain product being bonded, such as readjusting the welding angle and weapon position, can additionally avoid porosity. Regular assessment of welds and immediate removal of any concerns determined throughout the welding process visit this website are necessary techniques to stop porosity and create top notch welds.
Value of Appropriate Welding Methods
Applying proper welding strategies is extremely important in ensuring the structural stability and top quality of welded joints, developing upon the structure of reliable porosity avoidance measures. Welding techniques straight impact the overall toughness and durability of the bonded framework. One vital aspect of proper welding More Info methods is keeping the proper heat input. Too much heat can lead to increased porosity due to the entrapment of gases in the weld pool. Alternatively, inadequate heat may lead to incomplete fusion, creating prospective weak points in the joint. In addition, making use of the appropriate welding parameters, such as voltage, current, and take a trip rate, is important for achieving audio welds with very little porosity.
Moreover, the choice of welding process, whether it be MIG, TIG, or stick welding, should straighten with the particular requirements of the project to make certain optimal results. Proper cleansing and preparation of the base steel, along with choosing the ideal filler material, are additionally vital elements of skilled welding strategies. official statement By sticking to these finest practices, welders can minimize the danger of porosity formation and generate high-grade, structurally audio welds.
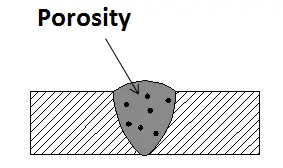
Evaluating and Quality Assurance Measures
Evaluating procedures are necessary to discover and protect against porosity in welding, making certain the toughness and resilience of the final item. Non-destructive testing methods such as ultrasonic testing, radiographic screening, and visual assessment are generally utilized to determine possible flaws like porosity.
Conducting pre-weld and post-weld assessments is likewise important in preserving high quality control requirements. Pre-weld assessments entail verifying the materials, tools settings, and sanitation of the workspace to avoid contamination. Post-weld examinations, on the other hand, examine the final weld for any flaws, including porosity, and verify that it fulfills specified standards. Applying an extensive top quality control strategy that includes complete screening procedures and assessments is extremely important to minimizing porosity issues and making sure the overall high quality of welded joints.
Verdict
To conclude, porosity in welding can be a common issue that impacts the quality of welds. By determining the common reasons for porosity and carrying out finest methods for avoidance, such as correct welding techniques and testing steps, welders can guarantee excellent quality and reputable welds. It is crucial to prioritize prevention methods to minimize the event of porosity and maintain the integrity of bonded frameworks.
Report this page